-
Call your bookkeeper – they might be able to add together all last year’s orders
-
Call the roaster – she can probably remember every mix and the volume
-
Pull out your tablet – check your previous volume, inventory and mix and place an order
-
Take a guess – After all, what could go wrong?
Hint: If you’ve got Cropster the answer is C. We know because a customer told us exactly this story and they made the order at a great price as a result.
Knowledge really is power when it comes to running your roastery. Production volume tracking is yet another area where it can bring real advantages. In Germany it’s required by law, but in most places it’s required to ensure a smoothly and profitably run ship. It’s key information for roasteries of all sizes which is why we continue to focus on and develop it. This month we release a new Production report and if you’re a Cropster user, you’re going to want to check it out. If you’re new to Cropster, you’ll definitely learn something about the advantages that your Cropster using competitors are gaining.
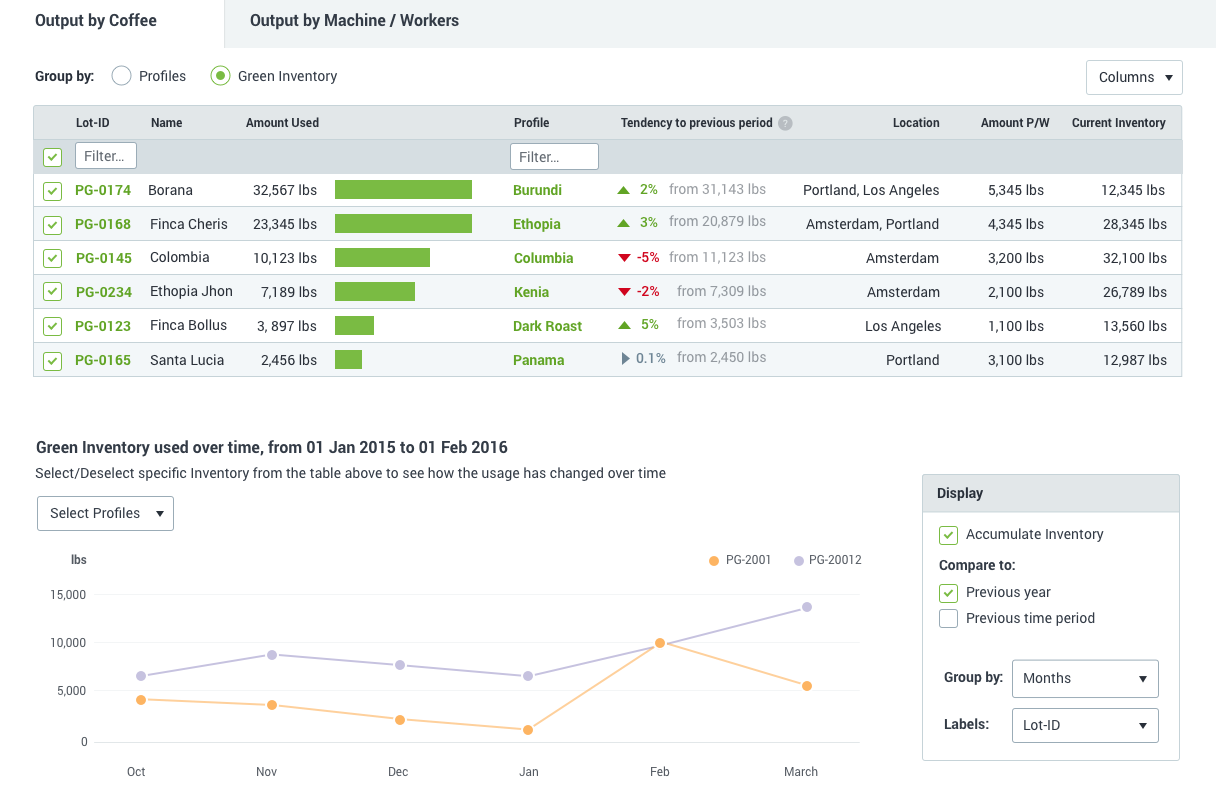
What’s new?
Well for starters, you can now easily see what you’ve produced and what’s remaining in your inventory at any given time during your production cycle. We know that is critical information and now it’s a few clicks away.
What’s produced and what’s remaining is cyclical information that follows your business cycle. As a result we have designed the report and accompanying charts for maximum impact to help with your business planning. What does that mean? You can compare any period against any other. Questions like “What were we doing last July vs. this July?” Easy. “How much did we purchase & produce last Christmas?” Also a few clicks away. How about making it dynamic so you can browse different periods? That’s in there too and it can be a real eye opener.
As you can imagine, this is information that can really help inform purchasing decisions. It will help with capacity planning. It can highlight niche areas where business is growing. It can show you output per roast machine or roaster. Best of all, it easily provides concrete numbers to drive investment decisions across your beans and your teams.
It’s worth mentioning these innovations are always the result of working directly with the Cropster community. If you are looking for information to help improve your decision making or you have a great idea you think would help improve your business processes please get in touch. There’s a lot of innovation to come!