Organic Operations in Coffee
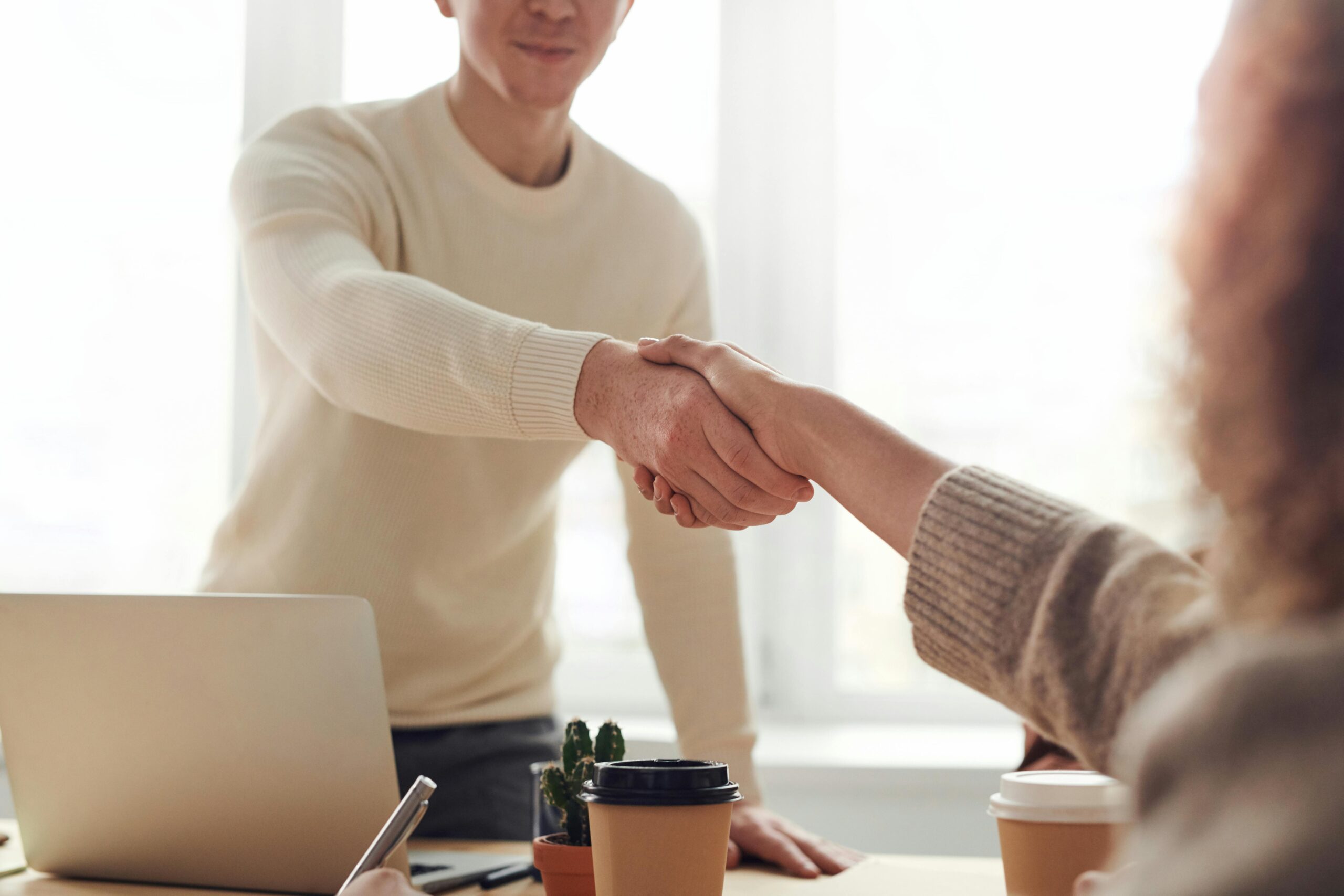
| Commerce
Table of Contents
It’s that time of year again. Some may dread it, some people may actually look forward to it, if for no other reason than to get it out of the way. The time you have been preparing for every day. It is the day of your Organic Audit! Maybe you have done this a dozen times, maybe this is your first. Either way, it is an important day for coffee companies that want to serve Organic certified coffee.
With the increase of Organic certified coffees entering the specialty world has come an increase in regulation and we are here to guide you through the processes. There are thousands of articles written on what is or is not organic, but we are here today to talk about how your coffee roasting operation can build out your workflows to maintain successful Organic processes.
Some regulations that are helpful to know:
- New FDA Organic regulations coming early 2026
- EU Organic Production
- Organic Code of Federal Regulations (US)
Your daily process
A successful organic process is going to be all about building good habits around the roastery. Keeping things tracked and clean is most important when handling Organic
- Starting your day
- There must be a cleaning (or purge) of your machine between organic certified coffees and nonorganic coffees to avoid cross contamination. Most people we work with choose to roast Organic first in the morning to avoid this purge roast.
- With our Scheduling tool, you can automatically set Organic roasts to go first in your day.
Cleaning
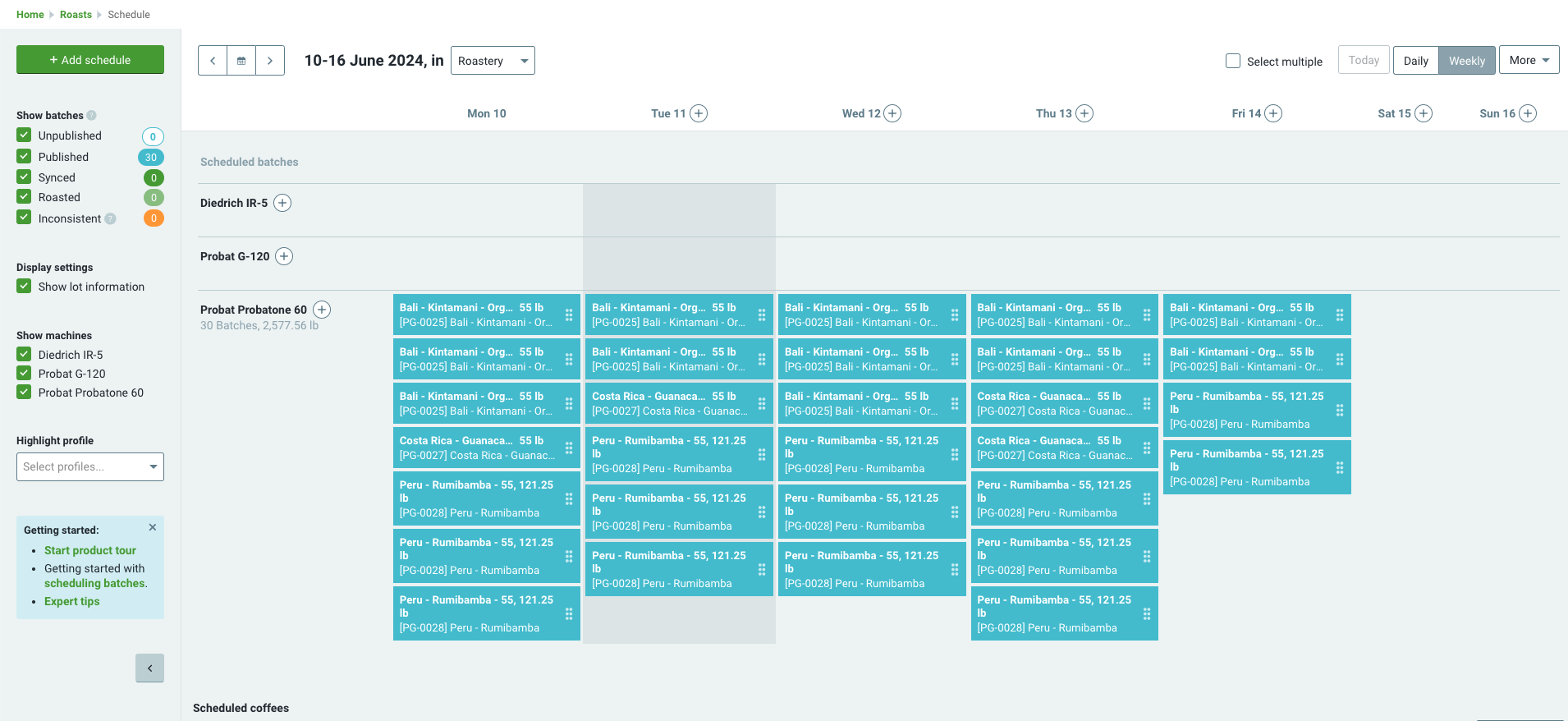
- The process here would be to clean, rinse, and sanitize. The cleaners you use do not need to be Organic. The main restriction will be that you need to rinse them and sanitize after washing. You will also need to provide a list of products you are using. The USDA has some great guidelines here
- With our Tasks functionality, you can create daily, weekly and monthly procedures to better help document your cleaning
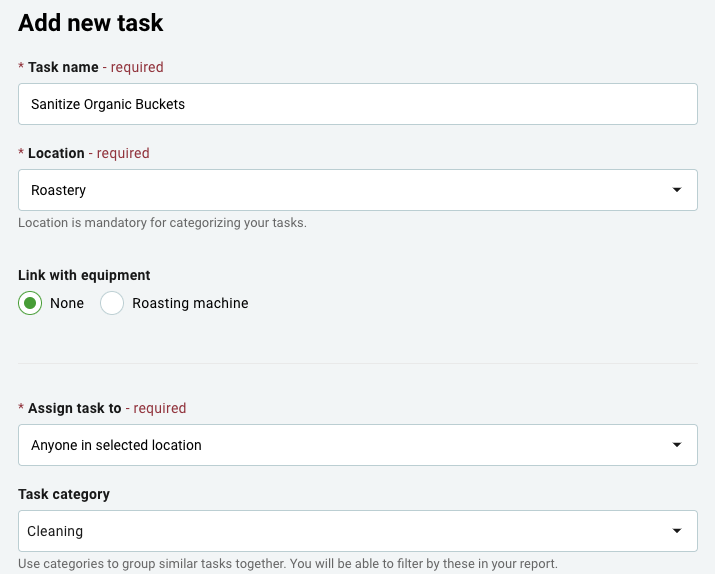
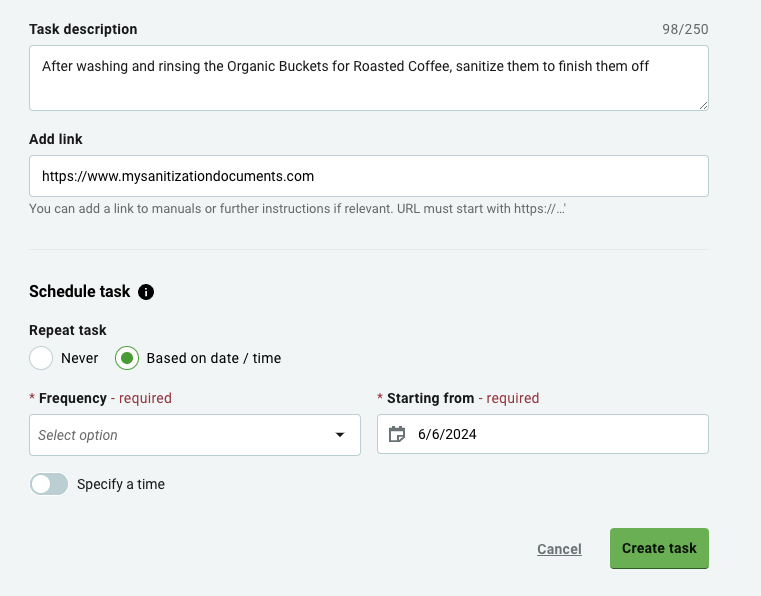
- Cleaning logs
- You will want to keep a log of when you are cleaning. It’s not important where this is stored, digitally or physically, but it is important to show your auditor that you are practicing consistent cleaning schedules. See tasks to see how you can track this with Cropster!
- Hair nets/beard nets
- No one wants to wear them, but the less opportunities for cross contamination, the better!
Storage
- Green and roasted Organic certified coffee will need to be stored separately from non-organic certified coffee. For green coffee, that is as simple as not stacking the two together, but it is good practice to have a designated organic area. One great way to do this for roasted coffee in your facility is by color coding your bins that you are storing them in throughout the day. If your team knows all red containers are for Organic certified coffee they can make streamlined and smart decisions.
Tracking
- You will want to show every step of the way in your coffee’s journey to you. This would be from your importer to you. Prior to that, your organic certified importer will have have it tracked!
- With Cropster, starting your green inventory from a sample, allows you to begin the tracking process before it ever arrives at your warehouse. You can even track your Pre-shipment samples. You can tag your coffee as Organic and create a simple process of presenting your data to your auditor
- Green Inventory also allows you to track your contracted coffee (via Locations) and show the moment you purchased a coffee and every movement in between.
- Using Cropster, you will be able to track every roast you do, how much is lost between green to roasted, and you’ll be able to pull reports to show exactly how much of each coffee you roasted! With the proper tagging of products, you can use the reporting features in Cropster to breeze through this part of your audit.
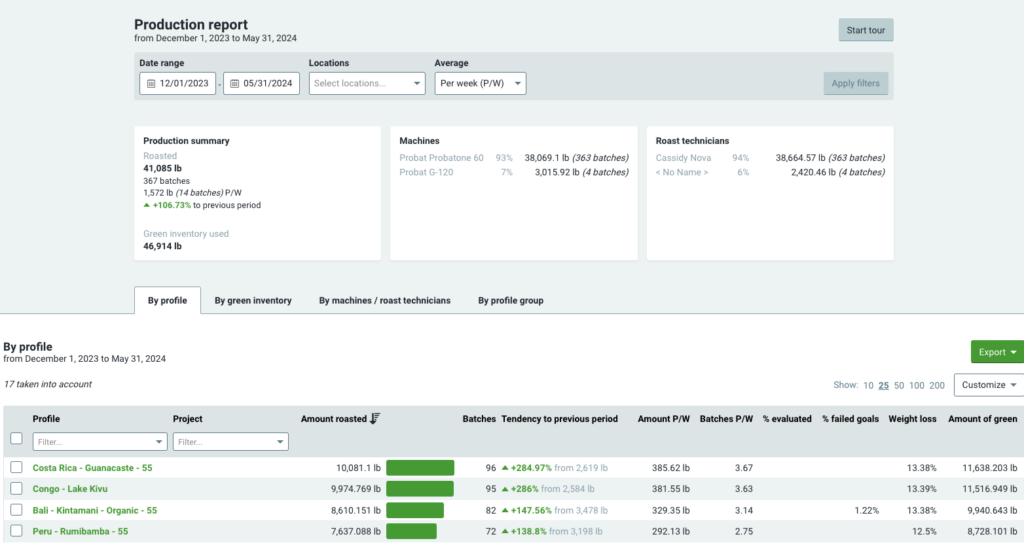
Traceability
- You will need to pull a mass balance report showing all organic coffee received and all organic coffee sold
- You will also potentially be asked to show an example of a specific month
- You will also need to be able to show the movement of this coffee every step of the way. Can you pull a random order from your sales and show the process of receiving the green inventory, when the coffee was roasted, and where it went? This is the process of creating traceability.
- Using our Traceability report, you can connect every roast you do to the orders it went into. You can also make note of each time coffee spilled, you pulled something for a cupping, or if coffee was removed from inventory for any reason
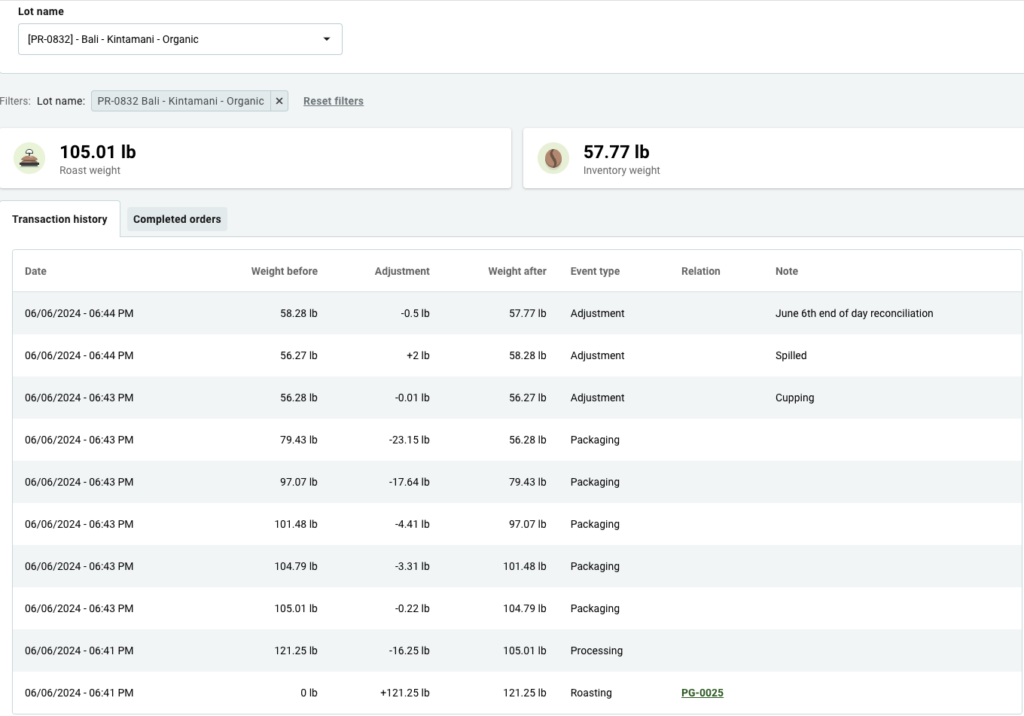
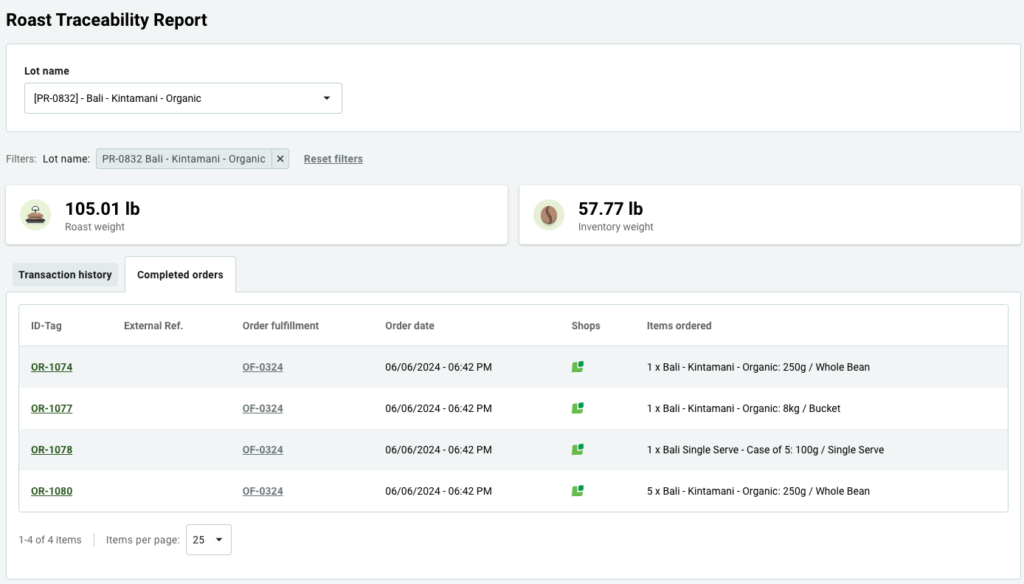
- Blends
- If you are choosing to blend an organic certified coffee with a non-organic certified coffee, you might have a large gap in those numbers. For that reason, you will want to track this! With our ability to track your inventory used for Pre and Post-roast blended coffee, you will be able to use Cropster to show these differences.
- Certification from your importer
- This is an easy step in the process. If your import is selling coffee as Organic certified, then they too are Organic certified! That means they follow their own set of practices similar to yours. With evidence of their certification and each of the coffees certification, you can breeze through this process.
Labeling
- You will want all of the Organic products you sell to be clearly labeled this way. A good practice at the roastery would be to use clearly labeled storage that is only used for Organic products. You should also have the word Organic in the title of the product in Cropster, your Accounting system, and physically written.
- For example, Sumatra Adsenia – Organic
Miscellaneous
- Visitors
- It is always good to keep a log of visitors that come through your facility. Be it for cross-contamination purposes or for memory or just to let people know you know they are there, this can be helpful and let your auditor know that you are in control of what/who is coming in your facility
- Office pet
- Of course only service animals are allowed in facilities producing food. Mainly, if you do have an office pet, you will want to have a clear area where they do not cross that will avoid cross-contamination. This might be installing a door where there wasn’t one before (or something like an industrial curtain wall)
- Cost Share Programs
- Be sure to check with your local state official programs to see how you can get a rebate on supporting Organic! CCOF California (available in all states and a good resource to find what states offer a rebate)
- Or just use a search engine and type “Organic Cost Share YOUR STATE”
- Or just use a search engine and type “Organic Cost Share YOUR STATE”
- Be sure to check with your local state official programs to see how you can get a rebate on supporting Organic! CCOF California (available in all states and a good resource to find what states offer a rebate)
Hopefully this is a good introduction to Organic processes and gives you an idea of what you will need to change in case you are looking to offer Organic products. We have a ton of experience here at Cropster, so reach out and ask us any questions you may have!
PS, these systems can also help with all sorts of other audits, like SQF, Deforestation, Rainforest alliance, and many more! Book a meeting with us today to learn more about how we can help you with your next audit!